Sagar Chisel Mortiser: Difference between revisions
No edit summary |
|||
(26 intermediate revisions by 3 users not shown) | |||
Line 1: | Line 1: | ||
{{Tool | |||
|image= | |||
== | |manufacturer=J. Sagar & Co. Halifax | ||
|model=1909 Model | |||
|obtained=[[Mortiser Pledge|Pledge Drive]], | |||
|obtaineddate=August 2016 | |||
|location=Workshop | |||
|team=Woodworking | |||
|induction=No | |||
|defunct= | |||
|defunctdate= | |||
}} | |||
{{photo}} | |||
[[File:Sagar Mortiser Ad 1909.jpeg|thumbnail|right]] | [[File:Sagar Mortiser Ad 1909.jpeg|thumbnail|right]] | ||
Manufactured by J. Sagar & Co. Halifax, based on promotional materials it appears to be based on a design already in production by 1909, and subsequently re-designed in the late | Manufactured by J. Sagar & Co. Halifax, based on promotional materials it appears to be based on a design already in production by 1909, and subsequently re-designed in the late 1920's to run on electrical rather than overhead belt power. Living history right here in the hackspace no less. | ||
=== What does it do? === | === What does it do? === | ||
Put simply, it is a drill for square holes. | Put simply, it is a drill for square holes. | ||
More comprehensively, A hollow chisel mortiser has | More comprehensively, A hollow chisel mortiser has an auger bit running inside a hollow, square chisel. Pulling the lever down brings the auger into the wood, cutting away the bulk of the material, before the chisel follows <sup>1</sup>/<sub>16</sub>" behind, taking away the material in the corners and forcing it up the augers flutes, to give a square hole. | ||
=== Why do we want to do that? === | === Why do we want to do that? === | ||
Line 18: | Line 27: | ||
It's hoped that this will open up some more ambitious and structural woodworking projects to all comers.<sup>[3]</sup> | It's hoped that this will open up some more ambitious and structural woodworking projects to all comers.<sup>[3]</sup> | ||
<div style="clear: both;"></div> | |||
== Standard Operating Procedure == | |||
First select dimensions and layout of the joints, appropriate to the timbers to be joined. | |||
=== Layout === | |||
# On each piece to be mortised, determine a "reference face" and mark it lightly in pencil. | |||
# Prepare a "rod" | |||
## Take a piece of scrap timber, ply or MDF, with at least one straight edge, and cut one end perpendicular to the straight edge. | |||
## Using a sharp, dark pencil and a steel rule or combination square, start from the perpendicular end making marks at the following distances: | |||
### Reference face to near side of mortise. | |||
### Reference face to far side of mortise. | |||
### End of timber to beginning of mortise. | |||
### End of timber to end of mortise | |||
### (if required) end of timber to end of haunch. | |||
## If space allows, clearly write what each mark refers to above it. | |||
# Use the rod to make marks on each piece indicating the distances. | |||
# Using a Set-Square or Combination Square join these marks to form a rectangle indicating material to be removed. | |||
# Cross hatch the area to be removed | |||
=== Setup === | |||
If the size of chisel required is not currently installed, you may need to change the tooling at this point. | |||
Where the chisel is too small and only one or two mortises are to be cut, it may be more sensible to cut the mortise along one side, then re-align the chisel and work the opposite side; where mortises of intermediate width between two chisel sizes are to be cut, this is the only method available. | |||
# Ensure the machine is switched off. | |||
# Approximately centre the table. | |||
# Raise the lever to bring the chisel clear of the bed. (N.B. Lifting the lever to vertical will result in the rack disengaging from the quadrant, allowing the mechanism to drop and potentially damaging it. '''Never lift the lever up completely vertical.''') | |||
# Place the work flat on the table and close the vice. | |||
# Lower the lever until the tip of the auger is just above the work. | |||
# Line up the edge of the chisel with the edges of the marked area (It may be necessary to use a small Set-Square placed on the workpiece to assist.) | |||
# If making a stub mortise, bring the lever down until the cutting lip of the auger touches the workpiece, and bring the depth stop down in contact with the workpiece, mark this position, then raise the depth stop up by the desired amount, using the mark to measure from, and secure the depth stop with the set-screw. | |||
=== Machining === | |||
See that the workpiece is aligned as in ''6.'' above. | |||
# Ensure the auger is not in contact with the workpiece. | |||
# Press the green button to turn on the motor. | |||
# Pull the lever down firmly and smoothly, taking care not to force the auger into the work faster than it can remove wood. | |||
# When the depth stop is in contact or the chisel has cut through to the opposite side, raise the lever to remove the chisel. | |||
# Move the chisel to the opposite end<sup>[4]</sup> of the mortice and align as per ''6.'' above, stopping the machine if necessary. | |||
# Repeat steps ''3.'' & ''4.'', moving workpiece along after each cut working toward the initial cut made in ''3.'' | |||
# Turn off the machine using the red button. | |||
# Clean up any chips generated. | |||
== Tool Change Procedure == | |||
== Installation Progress == | == Installation Progress == | ||
The machine is now in position, | The machine is now in position, and operational in a provisional manner, new tooling, a coat of paint and some minor improvement work will be carried out as ongoing [https://en.m.wikipedia.org/wiki/Total_productive_maintenance TPM]. | ||
The bolt which secures the chisel in position, unfortunately seized and subsequently sheered on attempting to free it. The remainder of the bolt has been drilled out, the residue of the threads removed with a tap, and a replacement (and spare) set-screw of the appropriate size (<sup>5</sup>/<sub>16</sub> Whitworth) has been sourced. | === Installation Work === | ||
==== Completed ==== | |||
The bolt which secures the chisel in position, unfortunately seized and subsequently sheered on attempting to free it. The remainder of the bolt has been drilled out, the residue of the threads removed with a tap, and a replacement (and spare) set-screw of the appropriate size (<sup>5</sup>/<sub>16</sub><sup>th</sup> Whitworth) has been sourced. | |||
Machine has been stripped, wire brushed, cleaned and coated with a thin coat of light oil. | |||
Threads on arm have been cleared with <sup>7</sup>/<sub>16</sub><sup>ths</sup> Whitworth tap. | |||
Ways on the table have been thoroughly cleaned, all ways have been lubricated using light oil (debatable as to whether way-lube would be beneficial or cause excessive buildup of sawdust). | |||
Damaged wiring to motor removed, motor has been stripped, all dust and chips removed, and the bearings checked, top bearing cover found to not be attached, needs 2 × 0BA 2" machine screws. sourced. | |||
Chisel and auger sharpened, fitted and adjusted. | |||
New depth stop machined from ½"<sup>O</sup>/<sub>D</sub> steel pipe from metalwork scrap bin. | |||
Chisel collet has significant damage, still serviceable as is but replacement best course of action long term. | |||
Auger collet has burr on bottom, could damage chisel holder assembly bearing surface during maintainance if not addressed. | |||
Z-axis travel rack missing tooth, has been replaced with two set screws, long term brazed-in replacement sensible. | |||
Sacrificial Table fitted using ply salvaged from box in the donation area. | |||
Old Cable Sheath removed, 25mm cable gland turned down and threaded to mate with existing connector on motor. | |||
Two M5 threaded holes made in Pillar to attach starter, starter wired to motor and plug (CEEform 16A 3ph+PE 4 Pin) | |||
Mating socket with inbuilt Isolator & RCD (25A 3ph+N with a resistive load between L2 & N) mounted to workshop ceiling and wiring run to workshop distro-board established. | |||
Tom G adjusted ways to remove play (developed after ways cleaned and lubricated). | |||
Rope attached to RSJ to limit movement of arm. | |||
==== Awaiting Completion ==== | |||
* Replace grease in motor bearings (at a minimum, lower bearing needs urgent top-up). | |||
* Fit some kind of limit to quadrant or lever to stop dropping of rack & motor | |||
* Machining | |||
** New collet for chisels from bar. | |||
*** Heat Treat new collet. | |||
** Remove Auger collet from spindle, turn chamfer on lower edge to remove burr (to protect bearing race chisel holder during future maintenance). | |||
** Hand-fit new tooth for rack and arrange to braze into position. | |||
* Re-Paint? | |||
** Sign-write lever with names of Pledges. | |||
=== Parts === | |||
==== Parts sourced: ==== | ==== Parts sourced: ==== | ||
* 2 × <sup>5</sup>/<sub>16</sub> BSW 2½" allen head set screws | * 2 × <sup>5</sup>/<sub>16</sub> BSW 2½" allen head set screws. | ||
* Depth stop (Turned from Mouse's scrap piping). | |||
* 12m of 5 core, 2.5mm<sup>2</sup> armoured cable. | |||
* 440v DOL Motor Starter, with 1.8-2.5A thermal overload. | |||
* ½ or ¾ ply - 2'6" by 8" — sacrificial table top. (Found in donations area) | |||
* 20A rotary isolator. | |||
* 20mm cable glands | |||
* 25mm cable glands | |||
* CEEform Plug , 16A 4 pin. (Provided from G4, after discussion with Matt Lloyd) | |||
* CEEform Socket, 16A 4 pin, 25A RCD, Rotary Isolator. (Provided from G4, after discussion with Matt Lloyd) | |||
==== Parts on order: ==== | ==== Parts on order: ==== | ||
==== Parts to order: ==== | ==== Parts to order: ==== | ||
* New tooling. | * New tooling. | ||
* 2 × 0BA 2" Machine Screw. | |||
* Paint. | |||
* 1½" round bar, EN47 or EN45 Steel | |||
* ¼" cast iron bar. | |||
=== Costs: === | === Costs: === | ||
Line 42: | Line 159: | ||
! Item !! Qty. !! Price per each !! Total cost !! Running total | ! Item !! Qty. !! Price per each !! Total cost !! Running total | ||
|- | |- | ||
| | | Morticer || 1 || £80.00 || £80.00 || £80.00 | ||
|- | |- | ||
| Van Hire || 1 || £95.00 || £95.00 || £175.00 | | Van Hire || 1 || £95.00 || £95.00 || £175.00 | ||
Line 55: | Line 172: | ||
|- | |- | ||
| DOL Starter || 1 || £35.49 || £35.49 || £278.38 | | DOL Starter || 1 || £35.49 || £35.49 || £278.38 | ||
|- | |||
| Cable Glands, 20mm || 14 || £0.364 || £5.09 || £283.47 | |||
|- | |||
| Cable Glands, 25mm || 2 || £0.825 ||£1.75 || £285.22 | |||
|} | |} | ||
== Footnotes == | == Footnotes == | ||
Line 93: | Line 182: | ||
# The keen eyed reader will note that in the above advertisment, Sagar suggest that being usable by "a lad" was one of the machine's selling points. | # The keen eyed reader will note that in the above advertisment, Sagar suggest that being usable by "a lad" was one of the machine's selling points. | ||
# Especially the author, who always enjoys mortising by hand to begin with, before getting part-way through and realising that He's ultimately rather lazy. | # Especially the author, who always enjoys mortising by hand to begin with, before getting part-way through and realising that He's ultimately rather lazy. | ||
# The reason for this step is that the chisel will cut straight down, when going through solid wood, but will be pushed very slightly towards the free space when working along a mortise. Best Practice is thus to, define both ends of the mortise as dead straight, by cutting through solid wood before removing the bulk of the waste is preferred. | |||
[[Category:Tools_and_Equipment]] | [[Category:Tools_and_Equipment]] |
Latest revision as of 06:28, 31 March 2021
Sagar Chisel Mortiser | |
---|---|
Manufacturer | J. Sagar & Co. Halifax |
Model | 1909 Model |
Obtained | Pledge Drive, (August 2016) |
Location | Workshop |
Team | Woodworking |
Induction Required | No |
Tools: all pages • list • Power Tools • Broken tools {{}} |
Please improve this page by adding a photo. Click to upload an image, help with using images can be found here. The talk page may contain suggestions about suitable images. |
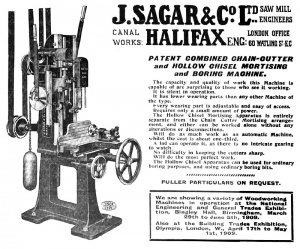
Manufactured by J. Sagar & Co. Halifax, based on promotional materials it appears to be based on a design already in production by 1909, and subsequently re-designed in the late 1920's to run on electrical rather than overhead belt power. Living history right here in the hackspace no less.
What does it do?
Put simply, it is a drill for square holes.
More comprehensively, A hollow chisel mortiser has an auger bit running inside a hollow, square chisel. Pulling the lever down brings the auger into the wood, cutting away the bulk of the material, before the chisel follows 1/16" behind, taking away the material in the corners and forcing it up the augers flutes, to give a square hole.
Why do we want to do that?
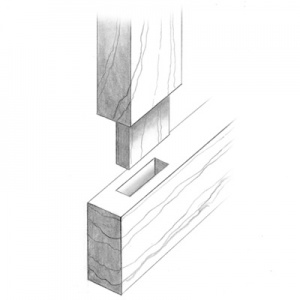
Mortise and Tenon joints in all their many forms, remain the strongest and most secure method of joining two pieces of wood.
Cutting a tight-fitting hole, in a piece of wood, which is dead square in all three dimensions, using nothing more than a mallet and chisel, requires a substantial amount of skill and practice;[1] not to mention a reasonable amount of effort; by contrast a chisel mortiser allows all this to be done with little more than a push of a button, turn of a wheel and pull of a lever.[2]
It's hoped that this will open up some more ambitious and structural woodworking projects to all comers.[3]
Standard Operating Procedure
First select dimensions and layout of the joints, appropriate to the timbers to be joined.
Layout
- On each piece to be mortised, determine a "reference face" and mark it lightly in pencil.
- Prepare a "rod"
- Take a piece of scrap timber, ply or MDF, with at least one straight edge, and cut one end perpendicular to the straight edge.
- Using a sharp, dark pencil and a steel rule or combination square, start from the perpendicular end making marks at the following distances:
- Reference face to near side of mortise.
- Reference face to far side of mortise.
- End of timber to beginning of mortise.
- End of timber to end of mortise
- (if required) end of timber to end of haunch.
- If space allows, clearly write what each mark refers to above it.
- Use the rod to make marks on each piece indicating the distances.
- Using a Set-Square or Combination Square join these marks to form a rectangle indicating material to be removed.
- Cross hatch the area to be removed
Setup
If the size of chisel required is not currently installed, you may need to change the tooling at this point. Where the chisel is too small and only one or two mortises are to be cut, it may be more sensible to cut the mortise along one side, then re-align the chisel and work the opposite side; where mortises of intermediate width between two chisel sizes are to be cut, this is the only method available.
- Ensure the machine is switched off.
- Approximately centre the table.
- Raise the lever to bring the chisel clear of the bed. (N.B. Lifting the lever to vertical will result in the rack disengaging from the quadrant, allowing the mechanism to drop and potentially damaging it. Never lift the lever up completely vertical.)
- Place the work flat on the table and close the vice.
- Lower the lever until the tip of the auger is just above the work.
- Line up the edge of the chisel with the edges of the marked area (It may be necessary to use a small Set-Square placed on the workpiece to assist.)
- If making a stub mortise, bring the lever down until the cutting lip of the auger touches the workpiece, and bring the depth stop down in contact with the workpiece, mark this position, then raise the depth stop up by the desired amount, using the mark to measure from, and secure the depth stop with the set-screw.
Machining
See that the workpiece is aligned as in 6. above.
- Ensure the auger is not in contact with the workpiece.
- Press the green button to turn on the motor.
- Pull the lever down firmly and smoothly, taking care not to force the auger into the work faster than it can remove wood.
- When the depth stop is in contact or the chisel has cut through to the opposite side, raise the lever to remove the chisel.
- Move the chisel to the opposite end[4] of the mortice and align as per 6. above, stopping the machine if necessary.
- Repeat steps 3. & 4., moving workpiece along after each cut working toward the initial cut made in 3.
- Turn off the machine using the red button.
- Clean up any chips generated.
Tool Change Procedure
Installation Progress
The machine is now in position, and operational in a provisional manner, new tooling, a coat of paint and some minor improvement work will be carried out as ongoing TPM.
Installation Work
Completed
The bolt which secures the chisel in position, unfortunately seized and subsequently sheered on attempting to free it. The remainder of the bolt has been drilled out, the residue of the threads removed with a tap, and a replacement (and spare) set-screw of the appropriate size (5/16th Whitworth) has been sourced.
Machine has been stripped, wire brushed, cleaned and coated with a thin coat of light oil.
Threads on arm have been cleared with 7/16ths Whitworth tap.
Ways on the table have been thoroughly cleaned, all ways have been lubricated using light oil (debatable as to whether way-lube would be beneficial or cause excessive buildup of sawdust).
Damaged wiring to motor removed, motor has been stripped, all dust and chips removed, and the bearings checked, top bearing cover found to not be attached, needs 2 × 0BA 2" machine screws. sourced.
Chisel and auger sharpened, fitted and adjusted.
New depth stop machined from ½"O/D steel pipe from metalwork scrap bin.
Chisel collet has significant damage, still serviceable as is but replacement best course of action long term.
Auger collet has burr on bottom, could damage chisel holder assembly bearing surface during maintainance if not addressed.
Z-axis travel rack missing tooth, has been replaced with two set screws, long term brazed-in replacement sensible.
Sacrificial Table fitted using ply salvaged from box in the donation area.
Old Cable Sheath removed, 25mm cable gland turned down and threaded to mate with existing connector on motor.
Two M5 threaded holes made in Pillar to attach starter, starter wired to motor and plug (CEEform 16A 3ph+PE 4 Pin)
Mating socket with inbuilt Isolator & RCD (25A 3ph+N with a resistive load between L2 & N) mounted to workshop ceiling and wiring run to workshop distro-board established.
Tom G adjusted ways to remove play (developed after ways cleaned and lubricated).
Rope attached to RSJ to limit movement of arm.
Awaiting Completion
- Replace grease in motor bearings (at a minimum, lower bearing needs urgent top-up).
- Fit some kind of limit to quadrant or lever to stop dropping of rack & motor
- Machining
- New collet for chisels from bar.
- Heat Treat new collet.
- Remove Auger collet from spindle, turn chamfer on lower edge to remove burr (to protect bearing race chisel holder during future maintenance).
- Hand-fit new tooth for rack and arrange to braze into position.
- New collet for chisels from bar.
- Re-Paint?
- Sign-write lever with names of Pledges.
Parts
Parts sourced:
- 2 × 5/16 BSW 2½" allen head set screws.
- Depth stop (Turned from Mouse's scrap piping).
- 12m of 5 core, 2.5mm2 armoured cable.
- 440v DOL Motor Starter, with 1.8-2.5A thermal overload.
- ½ or ¾ ply - 2'6" by 8" — sacrificial table top. (Found in donations area)
- 20A rotary isolator.
- 20mm cable glands
- 25mm cable glands
- CEEform Plug , 16A 4 pin. (Provided from G4, after discussion with Matt Lloyd)
- CEEform Socket, 16A 4 pin, 25A RCD, Rotary Isolator. (Provided from G4, after discussion with Matt Lloyd)
Parts on order:
Parts to order:
- New tooling.
- 2 × 0BA 2" Machine Screw.
- Paint.
- 1½" round bar, EN47 or EN45 Steel
- ¼" cast iron bar.
Costs:
Item | Qty. | Price per each | Total cost | Running total |
---|---|---|---|---|
Morticer | 1 | £80.00 | £80.00 | £80.00 |
Van Hire | 1 | £95.00 | £95.00 | £175.00 |
Fuel | 1 | £20.03 | £20.03 | £195.03 |
BSW Bolts | 2 | £1.50 | £3.00 | £198.03 |
3 Ph Cable | 12m | £2.78 | £33.36 | £231.39 |
Isolator | 1 | £11.50 | £11.50 | £242.89 |
DOL Starter | 1 | £35.49 | £35.49 | £278.38 |
Cable Glands, 20mm | 14 | £0.364 | £5.09 | £283.47 |
Cable Glands, 25mm | 2 | £0.825 | £1.75 | £285.22 |
Footnotes
- Indeed, it is not enough to develop the skill once, regular practice is essential to continue making a good job of it.
- The keen eyed reader will note that in the above advertisment, Sagar suggest that being usable by "a lad" was one of the machine's selling points.
- Especially the author, who always enjoys mortising by hand to begin with, before getting part-way through and realising that He's ultimately rather lazy.
- The reason for this step is that the chisel will cut straight down, when going through solid wood, but will be pushed very slightly towards the free space when working along a mortise. Best Practice is thus to, define both ends of the mortise as dead straight, by cutting through solid wood before removing the bulk of the waste is preferred.