Superbox CNC Router: Difference between revisions
mNo edit summary |
mNo edit summary |
||
Line 4: | Line 4: | ||
The CNC Mill was acquire from Wireless Things in 2016 after there close. The machine is quite unique in having a dual Y axis stepper setup however this does require the that startup procedure for homeing is carefully followed<br/> | The CNC Mill was acquire from Wireless Things in 2016 after there close. The machine is quite unique in having a dual Y axis stepper setup however this does require the that startup procedure for homeing is carefully followed<br/> | ||
Working area for the mill is | Working area for the mill is 375mm x 375mm x 150mm<br/> | ||
Max feed rate is 1900mm/min<br/> | Max feed rate is 1900mm/min<br/> | ||
The spindle is an Kress 1050 FME with manual speed control from 10,000 to 29,000 RPM<br/> | The spindle is an Kress 1050 FME with manual speed control from 10,000 to 29,000 RPM<br/> | ||
The mill PC is running LinuxCNC with the <code>Gmoccapy</code> interface <br/> | The mill PC is running LinuxCNC with the <code>Gmoccapy</code> interface <br/> | ||
Line 19: | Line 18: | ||
= | =Operation Instructions= | ||
==Turn on== | ==Turn on== | ||
Turn on the monitor, PC and Control box<br/> | Turn on the monitor, PC and Control box<br/> | ||
[[File:Control Box.jpg|300px|thumb]] | [[File:Control Box.jpg|300px|thumb|none]] | ||
The PC should auto boot into linux and automaticly log in to the <code>nottinghack</code> account, if not the password is <code>hackspace</code><br/> | The PC should auto boot into linux and automaticly log in to the <code>nottinghack</code> account, if not the password is <code>hackspace</code><br/> | ||
Once in you should see the following desktop, click on the <code>Launch CNC</code> icon to start LinuxCNC<br/> | Once in you should see the following desktop, click on the <code>Launch CNC</code> icon to start LinuxCNC<br/> | ||
[[File:01_Launch_CNC.png| | [[File:01_Launch_CNC.png|300px|thumb|none]] | ||
==Launch== | ==Launch== | ||
Your should now see the <code>Gmoccapy</code> interface to LinuxCNC<br/> | Your should now see the <code>Gmoccapy</code> interface to LinuxCNC<br/> | ||
If you get an error message restart the pc and try again<br/> | If you get an error message restart the pc and try again<br/> | ||
[[File:02 Linux CNC Started.png| | [[File:02 Linux CNC Started.png|300px|thumb|none]] | ||
==eStops== | ==eStops== | ||
Make sure the physical eStop's have been cleared and the eStop light on the control box is out<br/> | Make sure the physical eStop's have been cleared and the eStop light on the control box is out<br/> | ||
Line 35: | Line 37: | ||
Turn on the machine by clicking the power button just below<br/> | Turn on the machine by clicking the power button just below<br/> | ||
The Interface should look like this<br/> | The Interface should look like this<br/> | ||
[[File:03 Reset eStop and Turn on.png| | [[File:03 Reset eStop and Turn on.png|300px|thumb|none]]] | ||
==Homing== | ==Homing== | ||
Line 41: | Line 43: | ||
To use the machine we need to be in <code>world</code> mode where we operate X,Y,Z axis, LinuxCNC automatically switch to world mode once all the joints have been homed, but it is '''important''' to only ever use the 'Home all' option as homing a single joint at a time will damage the Y axis.<br/> | To use the machine we need to be in <code>world</code> mode where we operate X,Y,Z axis, LinuxCNC automatically switch to world mode once all the joints have been homed, but it is '''important''' to only ever use the 'Home all' option as homing a single joint at a time will damage the Y axis.<br/> | ||
To open the <code>Home menu</code> click the icon in the bottom left corner of the interface. (Target and three arrows)<br> | To open the <code>Home menu</code> click the icon in the bottom left corner of the interface. (Target and three arrows)<br> | ||
[[File:04 Home menu.png| | [[File:04 Home menu.png|300px|thumb|none]]] | ||
In the bottom menu now click the Home all Icon (far left)<br/> | In the bottom menu now click the Home all Icon (far left)<br/> | ||
'''Warning''' This will cause the machine to move, please make sure all axis are free and clear to move and nothing is in the way for the spindle head<br> | '''Warning''' This will cause the machine to move, please make sure all axis are free and clear to move and nothing is in the way for the spindle head<br> | ||
[[File:05 Home all joints.png| | [[File:05 Home all joints.png|300px|thumb|none]]] | ||
The machine should now be ready to go<br/> | The machine should now be ready to go<br/> | ||
'''Important''' There should be no need to home the machine again however if you need to (due to axis slip or a crash) please close LinuxCNC first and start again, as homing in <code>world</code> mode is not supported. | '''Important''' There should be no need to home the machine again however if you need to (due to axis slip or a crash) please close LinuxCNC first and start again, as homing in <code>world</code> mode is not supported. | ||
[[File:06 Ready to go.png| | [[File:06 Ready to go.png|300px|thumb|none]]] | ||
==Loading G Code== | |||
After you have homed the machine using the instructions above, Click "Enter auto mode to run programs" on the right hand side menu. | |||
On the bottom row of icons you will see a folder icon. Click this to navigate to your ".ngc" G-Code file. | |||
<gallery> | |||
File:Screenshot - 021218 1.png|1 | |||
File:Screenshot - 021218 2.png|2 | |||
</gallery> | |||
==Setting G54 and tool offset== | |||
G54 Is used a constant value used to provide the offset for the local coordinate system. I.e. Used to tell the CNC software where you have secured your work-piece to the table. | |||
It needs to be set before any program is run! | |||
To set it, | |||
# Enter Manual Jogging mode by pressing the appropriate button on the right hand side or pressing F3 on the keyboard. | |||
# Use the control arrows to move the gantry so that the centre of the tool is sitting on the point where (X,Y,Z) is (0,0,0) on your CAD model. | |||
# Make a note of the Abs readings on the DRO (Green text on the top right) | |||
# Open the MDI mode of GMOCCAPY program by pressing the appropriate button on the right hand side or pressing F5. | |||
# Set G54 by running the following command | |||
'''G10 L2 P1 X??? Y??? Z???''' | |||
Where ??? are the coordinates you noted down in step 3. | |||
You should see the preview of your g-code shift to the new location. | |||
==Running a job== | |||
Once G54 is set and the code is loaded simply press the Play button located in the "Auto Mode" menu. | |||
Don't leave the job unattended and be ready with the Hoover as a lot of sawdust can be produced. | |||
ENSURE YOU HAVE EASY ACCESS TO THE EMERGENCY STOP | |||
=Spindle= | =Spindle= | ||
[[File:Spindle controls.jpg|450px|thumb]] | [[File:Spindle controls.jpg|450px|thumb|none]] | ||
The spindles speed control is manually controlled via the dial on the top.<br/> | The spindles speed control is manually controlled via the dial on the top.<br/> | ||
Power is controlled via LinuxCNC during operation but there is also a slide switch in the side of the spindle, this should be left on at all times<br/> | Power is controlled via LinuxCNC during operation but there is also a slide switch in the side of the spindle, this should be left on at all times<br/> | ||
Line 93: | Line 132: | ||
[[File:20mmbedplate.pdf]] | [[File:20mmbedplate.pdf]] | ||
= | =Suitable materials= | ||
* Most woods | |||
* Most plastics | |||
* Others with extreme caution | |||
I have tried soft woods such as Pine with great results. | |||
Plywood also works very well for simple profiles but can chip easily if you are doing moulding operations. | |||
Other materials may work, If you manage to cut anything like aluminium or other similarly hard materials then PLEASE share your projects and settings. | |||
=Exporting from Fusion360= | |||
= | |||
Once you have set up your tool paths using the CAM tools in Fusion you can export the setup using the Enhanced Machine Control post processor built in to [[Fusion 360]]. | |||
A good place to start if you're not sure with CNC programming is the [https://www.youtube.com/user/saunixcomp/| NYCCNC Youtube channel]. | |||
Line 138: | Line 153: | ||
If you have a project that uses this tool please add it to this list. | If you have a project that uses this tool please add it to this list. | ||
It would be great to see what other people are using the CNC Mill for! | It would be great to see what other people are using the CNC Mill for! | ||
[[Category:Tools_and_Equipment]] | [[Category:Tools_and_Equipment]] |
Revision as of 01:35, 22 December 2018
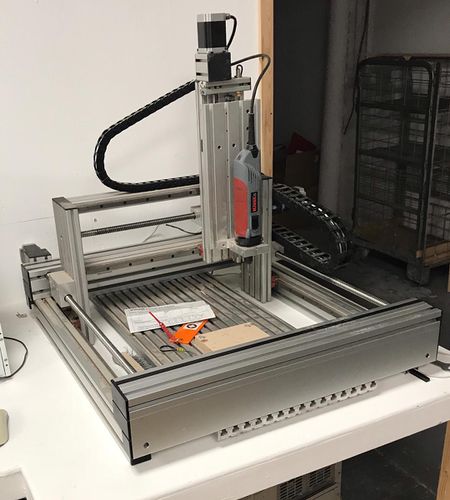
About
The CNC Mill was acquire from Wireless Things in 2016 after there close. The machine is quite unique in having a dual Y axis stepper setup however this does require the that startup procedure for homeing is carefully followed
Working area for the mill is 375mm x 375mm x 150mm
Max feed rate is 1900mm/min
The spindle is an Kress 1050 FME with manual speed control from 10,000 to 29,000 RPM
The mill PC is running LinuxCNC with the Gmoccapy
interface
Gmocappy is a more friendly skin/interface to LinuxCNC than the default Axis
some people might be more familiar.
More info about Gmocappy can be found here http://www.linuxcnc.org/docs/2.7/html/gui/gmoccapy.html
Slightly older video but might be useful https://www.youtube.com/watch?v=O5B-s3uiI6g&t=219s
Y Axis
Due to the gantry Y axis having a dual stepper drive the mill is using a development version of LinuxCNC 2.8, which can currently can cause some issue on start up.
The Y axis is also fitted with two stops, the second of which was designed and add but the hackspace to help in keeping the Y axis homing square to the X axis
Operation Instructions
Turn on
Turn on the monitor, PC and Control box
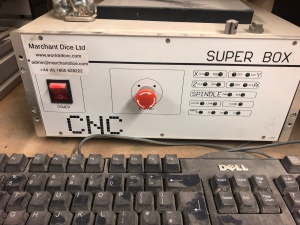
The PC should auto boot into linux and automaticly log in to the nottinghack
account, if not the password is hackspace
Once in you should see the following desktop, click on the Launch CNC
icon to start LinuxCNC
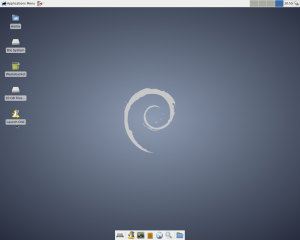
Launch
Your should now see the Gmoccapy
interface to LinuxCNC
If you get an error message restart the pc and try again
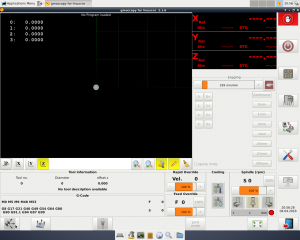
eStops
Make sure the physical eStop's have been cleared and the eStop light on the control box is out
Reset The linuxCNC soft eStop by clicking the red hand in the top right corner
Turn on the machine by clicking the power button just below
The Interface should look like this
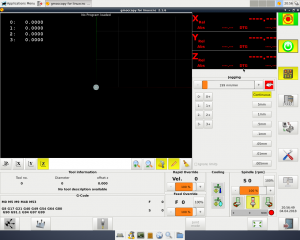
]
Homing
The machine starts-up in joint
mode, in this mode it is possible to move each stepper motor (0,1,2,3) independently but doing so can damage the Y axis
To use the machine we need to be in world
mode where we operate X,Y,Z axis, LinuxCNC automatically switch to world mode once all the joints have been homed, but it is important to only ever use the 'Home all' option as homing a single joint at a time will damage the Y axis.
To open the Home menu
click the icon in the bottom left corner of the interface. (Target and three arrows)
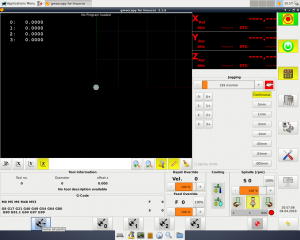
]
In the bottom menu now click the Home all Icon (far left)
Warning This will cause the machine to move, please make sure all axis are free and clear to move and nothing is in the way for the spindle head
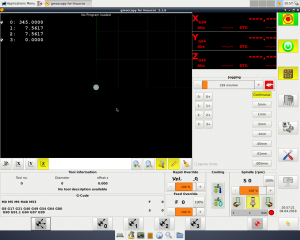
]
The machine should now be ready to go
Important There should be no need to home the machine again however if you need to (due to axis slip or a crash) please close LinuxCNC first and start again, as homing in world
mode is not supported.
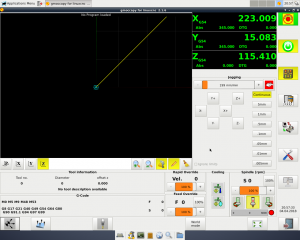
]
Loading G Code
After you have homed the machine using the instructions above, Click "Enter auto mode to run programs" on the right hand side menu. On the bottom row of icons you will see a folder icon. Click this to navigate to your ".ngc" G-Code file.
-
1
-
2
Setting G54 and tool offset
G54 Is used a constant value used to provide the offset for the local coordinate system. I.e. Used to tell the CNC software where you have secured your work-piece to the table. It needs to be set before any program is run!
To set it,
- Enter Manual Jogging mode by pressing the appropriate button on the right hand side or pressing F3 on the keyboard.
- Use the control arrows to move the gantry so that the centre of the tool is sitting on the point where (X,Y,Z) is (0,0,0) on your CAD model.
- Make a note of the Abs readings on the DRO (Green text on the top right)
- Open the MDI mode of GMOCCAPY program by pressing the appropriate button on the right hand side or pressing F5.
- Set G54 by running the following command
G10 L2 P1 X??? Y??? Z??? Where ??? are the coordinates you noted down in step 3.
You should see the preview of your g-code shift to the new location.
Running a job
Once G54 is set and the code is loaded simply press the Play button located in the "Auto Mode" menu. Don't leave the job unattended and be ready with the Hoover as a lot of sawdust can be produced.
ENSURE YOU HAVE EASY ACCESS TO THE EMERGENCY STOP
Spindle
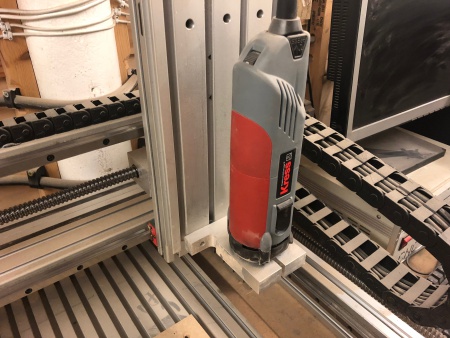
The spindles speed control is manually controlled via the dial on the top.
Power is controlled via LinuxCNC during operation but there is also a slide switch in the side of the spindle, this should be left on at all times
Dial | RPM |
---|---|
1 | 10,000 |
2 | 12.600 |
3 | 17,000 |
4 | 21,000 |
5 | 25,000 |
6 | 29,000 |
There is a spindle lock button to aid with tool and collet changes
We have the following collets, currently stored underneath the monitor for the CNC Computer.
1/8" (3.17mm) |
6mm |
8mm |
10mm |
Bed
The bed is made form PT25 profile Aluminium at 375mm wide
This gives slots every 25mm for fixing
File:20mmbedplate.pdf
Suitable materials
- Most woods
- Most plastics
- Others with extreme caution
I have tried soft woods such as Pine with great results. Plywood also works very well for simple profiles but can chip easily if you are doing moulding operations. Other materials may work, If you manage to cut anything like aluminium or other similarly hard materials then PLEASE share your projects and settings.
Exporting from Fusion360
Once you have set up your tool paths using the CAM tools in Fusion you can export the setup using the Enhanced Machine Control post processor built in to Fusion 360. A good place to start if you're not sure with CNC programming is the NYCCNC Youtube channel.
Example Projects
If you have a project that uses this tool please add it to this list. It would be great to see what other people are using the CNC Mill for!