Superbox CNC Router: Difference between revisions
m →Y Axis |
No edit summary |
||
Line 4: | Line 4: | ||
|manufacturer=Marchant Dice | |manufacturer=Marchant Dice | ||
|location=CNC Area | |location=CNC Area | ||
|obtained=2016 | |obtained=Acquired from Wireless Things after their close | ||
|obtaineddate=2016 | |||
|induction=No | |induction=No | ||
}} | }}The CNC Mill is a versatile tool that can cut a wide variety of materials. The machine has 3 degrees of freedom meaning that unlike the [[Laser Cutter]], which can only cut 2D Shapes, the CNC Mill can carve shapes in 3 dimensions if you can provide the tool paths to drive it. It does not require an induction to use, but help is available if you need it! Contact the #CNC channel on [[Slack]] if you need help. | ||
The CNC Mill | |||
We operate a bring-your-own-bits policy for this machine due to the high likelihood of broken tools. Links to buy tools are available on the [[Suppliers#Milling|Suppliers]] page. | |||
{{TOC limit|3}} | |||
==Overview== | |||
{| class="wikitable" width=90% | |||
! width=20% | Parameter | |||
! colspan="3" | Value | |||
|- | |||
| style="background-color:#efefef;" rowspan="2" | Working Area | |||
| style="background-color:#efefef;" | X | |||
| style="background-color:#efefef;" | Y | |||
| style="background-color:#efefef;" | Z | |||
|- | |||
| 345mm | |||
| 345mm | |||
| 150mm | |||
|- | |||
| style="background-color:#efefef;" | Maximum Feed Rate | |||
| colspan="3" | 1900mm/min | |||
|- | |||
| style="background-color:#efefef;" | Spindle | |||
| colspan="3" | Kress 1050 FME | |||
|- | |||
| style="background-color:#efefef;" | Control Software | |||
| colspan="3" | [http://linuxcnc.org/ LinuxCNC] | |||
|- | |||
| style="background-color:#efefef;" | Control Interface | |||
| colspan="3" | [http://www.linuxcnc.org/docs/2.7/html/gui/gmoccapy.html Gmoccapy] | |||
|- | |||
| style="background-color:#efefef;" | Control Hardware | |||
| colspan="3" | Superbox 2.8 | |||
|} | |||
===Software=== | |||
LinuxCNC, with the Gmoccapy interface, is the control software that we use to drive the tool. There is a dedicated computer hooked up to the machine for this purpose. | |||
LinuxCNC reads G-Code in the .ngc format. You can use any CAM (Computer Aided Manufacture) package you like to create G-Code at home or on the computers in the [[Blue Room]]. | |||
Slightly older video about Gmoccapy but might be useful to familiarize yourself: https://www.youtube.com/watch?v=O5B-s3uiI6g&t=219s | |||
Slightly older video but might be useful: https://www.youtube.com/watch?v=O5B-s3uiI6g&t=219s | |||
==Y Axis== | ===Y Axis=== | ||
The machine is quite unique in having a dual Y axis stepper setup; however, this does require that the start-up procedure for homeing is carefully followed. | |||
==Spindle== | Due to the gantry Y axis having a dual stepper drive the mill is using a development version of LinuxCNC 2.8, which can currently can cause some issue on start up. The Y axis is also fitted with two stops, the second of which was designed and added by the hackspace to help in keeping the Y axis homing square to the X axis | ||
===Spindle=== | |||
[[File:Spindle controls.jpg|300px|thumb|right|Black dial (Top Left) controls speed]] | [[File:Spindle controls.jpg|300px|thumb|right|Black dial (Top Left) controls speed]] | ||
The Spindle is a Kress 1050 FME. Its speed is manually controlled via the black dial on the top. It is a good idea to set the spindle speed whilst the spindle is stopped to minimize the operator reaching over the moving machine. | The Spindle is a Kress 1050 FME. Its speed is manually controlled via the black dial on the top. It is a good idea to set the spindle speed whilst the spindle is stopped to minimize the operator reaching over the moving machine. | ||
Line 50: | Line 80: | ||
There is a spindle lock button to aid with tool and collet changes<br/> | There is a spindle lock button to aid with tool and collet changes<br/> | ||
===Collets=== | ====Collets==== | ||
We have the following collets available, currently stored underneath the monitor for the CNC Computer. | We have the following collets available, currently stored underneath the monitor for the CNC Computer. | ||
Line 64: | Line 94: | ||
|} | |} | ||
==Bed== | ===Bed=== | ||
The bed is made from PT25 profile Aluminium at 375mm wide<br/> | The bed is made from PT25 profile Aluminium at 375mm wide<br/> | ||
This gives slots every 25mm for fixing. | This gives slots every 25mm for fixing. | ||
Line 73: | Line 103: | ||
The T-Slot nuts will accept an M6 bolt. | The T-Slot nuts will accept an M6 bolt. | ||
==Suitable materials== | ===Suitable materials=== | ||
* Most woods | * Most woods | ||
Line 81: | Line 111: | ||
* Others with extreme caution | * Others with extreme caution | ||
This machine is best suited to | This machine is best suited to soft materials due to its aluminium frame. Soft woods, such as Pine, can be cut easily with great results. Plywood is a cheap material that can be used to produce simple profiles quickly but is likely to chip if you are doing any moulding operations. Other materials may work with extreme caution; YouTube videos are a good place to start. | ||
If you are planning to cut hard materials materials have a couple of spare tools to hand, as you will no doubt break one. Also, do not underestimate the amount of time it will take to clean the machine after the cut. Please leave the machine as you would like to find it. | If you are planning to cut hard materials materials have a couple of spare tools to hand, as you will no doubt break one. Also, do not underestimate the amount of time it will take to clean the machine after the cut. Please leave the machine as you would like to find it. | ||
=Generating G-Code= | ==Generating G-Code== | ||
To control the tool you will need to feed it instructions. This is done through G-Code! | To control the tool you will need to feed it instructions. This is done through G-Code! | ||
There are more than a few options available for generating G-Code. Each has different pros & cons and each requires a different set of skills to operate. | There are more than a few options available for generating G-Code. Each has different pros & cons and each requires a different set of skills to operate. | ||
Line 94: | Line 124: | ||
File:Fusion 360 Toolpath Example.png|Tool paths from [[Fusion 360]]|link=Han Solo in Carbonite | File:Fusion 360 Toolpath Example.png|Tool paths from [[Fusion 360]]|link=Han Solo in Carbonite | ||
</gallery> | </gallery> | ||
==For Beginners== | ===For Beginners=== | ||
Inventables' [[Easel]] is a 2.5D online CAM package that has a friendly GUI and only requires two small alterations to the code to enable it to function with our machine. | Inventables' [[Easel]] is a 2.5D online CAM package that has a friendly GUI and only requires two small alterations to the code to enable it to function with our machine. | ||
==For Enthusiasts/ Advanced Users== | ===For Enthusiasts/ Advanced Users=== | ||
[[Fusion 360]] is a great free software package that has tons of CAM functionality built in. | [[Fusion 360]] is a great free software package that has tons of CAM functionality built in. | ||
Once you have set up your tool paths using the CAM tools in Fusion you can export the setup using the Enhanced Machine Control post processor built in to [[Fusion 360]]. | Once you have set up your tool paths using the CAM tools in Fusion you can export the setup using the Enhanced Machine Control post processor built in to [[Fusion 360]]. | ||
A good place to start if you're not sure with CNC programming via Fusion 360 is the [https://www.youtube.com/user/saunixcomp/| NYCCNC Youtube channel]. | A good place to start if you're not sure with CNC programming via Fusion 360 is the [https://www.youtube.com/user/saunixcomp/| NYCCNC Youtube channel]. | ||
=Operation Instructions= | ==Operation Instructions== | ||
==Safety== | ===Safety=== | ||
This is a dangerous tool and should be treated as such. | This is a dangerous tool and should be treated as such. | ||
Your safety is your own responsibility. As a guideline, you should wear as a minimum: | Your safety is your own responsibility. As a guideline, you should wear as a minimum: | ||
Line 114: | Line 144: | ||
:This machine is seriously loud, you must sit very near to it to monitor the job while it’s running and it’s not uncommon for a cutting cycle to be 30 minutes or longer. Hearing damage is a very real risk. Make sure you also warn others in the CNC room of this too. | :This machine is seriously loud, you must sit very near to it to monitor the job while it’s running and it’s not uncommon for a cutting cycle to be 30 minutes or longer. Hearing damage is a very real risk. Make sure you also warn others in the CNC room of this too. | ||
==Loading your tool== | ===Loading your tool=== | ||
When loading your tool you need to ensure that as much of the shank is contained within the collet as possible. The only exception to this rule is if the job you are running requires a deep cut; then you will need the tool to stick out further. | When loading your tool you need to ensure that as much of the shank is contained within the collet as possible. The only exception to this rule is if the job you are running requires a deep cut; then you will need the tool to stick out further. | ||
Line 124: | Line 154: | ||
{{#widget:YouTube|id=LiYze5CjDFU|width=640}} | {{#widget:YouTube|id=LiYze5CjDFU|width=640}} | ||
==Turn on== | ===Turn on=== | ||
Turn on the monitor, PC and Control box<br/> | Turn on the monitor, PC and Control box<br/> | ||
Line 138: | Line 168: | ||
{{note|If you get an error message or the computer is frozen, restart the PC and try again.}} | {{note|If you get an error message or the computer is frozen, restart the PC and try again.}} | ||
==Emergency Stops== | ===Emergency Stops=== | ||
Make sure the physical eStop's have been cleared by twisting them and check that the eStop light on the control box is out. | Make sure the physical eStop's have been cleared by twisting them and check that the eStop light on the control box is out. | ||
Line 150: | Line 180: | ||
</gallery> | </gallery> | ||
==Homing== | ===Homing=== | ||
The machine starts-up in <code>joint</code> mode, in this mode it is possible to move each stepper motor (0,1,2,3) independently but doing so can damage the Y axis. | The machine starts-up in <code>joint</code> mode, in this mode it is possible to move each stepper motor (0,1,2,3) independently but doing so can damage the Y axis. | ||
Line 171: | Line 201: | ||
</gallery> | </gallery> | ||
==Loading G Code== | ===Loading G Code=== | ||
After you have homed the machine using the instructions above, Click "Enter auto mode to run programs" on the right hand side menu. | After you have homed the machine using the instructions above, Click "Enter auto mode to run programs" on the right hand side menu. | ||
Line 182: | Line 212: | ||
</gallery> | </gallery> | ||
==Setting Zero== | ===Setting Zero=== | ||
G54 is a constant value that is used to provide the offset for the local coordinate system. I.e. It is used to tell the CNC software where you have secured your work-piece to the table (Set Zero). It needs to be set before any program is run! | G54 is a constant value that is used to provide the offset for the local coordinate system. I.e. It is used to tell the CNC software where you have secured your work-piece to the table (Set Zero). It needs to be set before any program is run! | ||
Line 198: | Line 228: | ||
If everything has been set correctly, you should see the preview of your G-Code shift to the correct location. | If everything has been set correctly, you should see the preview of your G-Code shift to the correct location. | ||
==Running a job== | ===Running a job=== | ||
Once G54 is set and the code is loaded simply press the Play button located in the "Auto Mode" menu. | Once G54 is set and the code is loaded simply press the Play button located in the "Auto Mode" menu. | ||
Line 205: | Line 235: | ||
{{note|'''ENSURE YOU HAVE EASY ACCESS TO THE EMERGENCY STOP'''}} | {{note|'''ENSURE YOU HAVE EASY ACCESS TO THE EMERGENCY STOP'''}} | ||
=Example Projects= | ==Example Projects== | ||
If you have a project that uses this tool please add it to this list. | If you have a project that uses this tool please add it to this list. | ||
Line 216: | Line 246: | ||
File:WW2 Prop Gold (4).jpg|WW2 Prop Gold|link=WW2 Prop Gold | File:WW2 Prop Gold (4).jpg|WW2 Prop Gold|link=WW2 Prop Gold | ||
</gallery> | </gallery> | ||
==See also== | ==See also== |
Revision as of 16:14, 17 April 2019
- See also: New CNC PC Pledge
Superbox CNC Router | |
---|---|
![]() | |
Manufacturer | Marchant Dice |
Obtained | Acquired from Wireless Things after their close (2016) |
Location | CNC Area |
Team | Tools |
Induction Required | No |
Tools: all pages • list • Power Tools • Broken tools {{}} |
The CNC Mill is a versatile tool that can cut a wide variety of materials. The machine has 3 degrees of freedom meaning that unlike the Laser Cutter, which can only cut 2D Shapes, the CNC Mill can carve shapes in 3 dimensions if you can provide the tool paths to drive it. It does not require an induction to use, but help is available if you need it! Contact the #CNC channel on Slack if you need help.
We operate a bring-your-own-bits policy for this machine due to the high likelihood of broken tools. Links to buy tools are available on the Suppliers page.
Overview
Parameter | Value | ||
---|---|---|---|
Working Area | X | Y | Z |
345mm | 345mm | 150mm | |
Maximum Feed Rate | 1900mm/min | ||
Spindle | Kress 1050 FME | ||
Control Software | LinuxCNC | ||
Control Interface | Gmoccapy | ||
Control Hardware | Superbox 2.8 |
Software
LinuxCNC, with the Gmoccapy interface, is the control software that we use to drive the tool. There is a dedicated computer hooked up to the machine for this purpose.
LinuxCNC reads G-Code in the .ngc format. You can use any CAM (Computer Aided Manufacture) package you like to create G-Code at home or on the computers in the Blue Room.
Slightly older video about Gmoccapy but might be useful to familiarize yourself: https://www.youtube.com/watch?v=O5B-s3uiI6g&t=219s
Y Axis
The machine is quite unique in having a dual Y axis stepper setup; however, this does require that the start-up procedure for homeing is carefully followed.
Due to the gantry Y axis having a dual stepper drive the mill is using a development version of LinuxCNC 2.8, which can currently can cause some issue on start up. The Y axis is also fitted with two stops, the second of which was designed and added by the hackspace to help in keeping the Y axis homing square to the X axis
Spindle
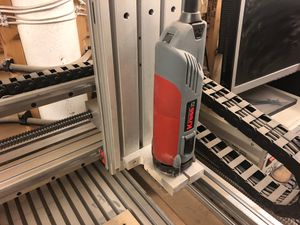
The Spindle is a Kress 1050 FME. Its speed is manually controlled via the black dial on the top. It is a good idea to set the spindle speed whilst the spindle is stopped to minimize the operator reaching over the moving machine.
Power to the spindle is controlled via LinuxCNC during operation; It will spin up once you start running the G-Code. There is a slide switch on the side of the spindle that should be left on at all times. If it is turned off the tool will simply crash into the work piece without cutting.
Dial | RPM |
---|---|
1 | 10,000 |
2 | 12.600 |
3 | 17,000 |
4 | 21,000 |
5 | 25,000 |
6 | 29,000 |
There is a spindle lock button to aid with tool and collet changes
Collets
We have the following collets available, currently stored underneath the monitor for the CNC Computer.
1/8" (3.17mm) |
6mm |
8mm |
10mm |
Bed
The bed is made from PT25 profile Aluminium at 375mm wide
This gives slots every 25mm for fixing.
We have a small selection of T-Slot nuts that will slide into these channels to provide clamping anchors. The T-Slot nuts will accept an M6 bolt.
Suitable materials
- Most woods
- Most plastics
- 6082 T6 Aluminium with caution
- Brass with caution
- Others with extreme caution
This machine is best suited to soft materials due to its aluminium frame. Soft woods, such as Pine, can be cut easily with great results. Plywood is a cheap material that can be used to produce simple profiles quickly but is likely to chip if you are doing any moulding operations. Other materials may work with extreme caution; YouTube videos are a good place to start.
If you are planning to cut hard materials materials have a couple of spare tools to hand, as you will no doubt break one. Also, do not underestimate the amount of time it will take to clean the machine after the cut. Please leave the machine as you would like to find it.
Generating G-Code
To control the tool you will need to feed it instructions. This is done through G-Code! There are more than a few options available for generating G-Code. Each has different pros & cons and each requires a different set of skills to operate.
For Beginners
Inventables' Easel is a 2.5D online CAM package that has a friendly GUI and only requires two small alterations to the code to enable it to function with our machine.
For Enthusiasts/ Advanced Users
Fusion 360 is a great free software package that has tons of CAM functionality built in. Once you have set up your tool paths using the CAM tools in Fusion you can export the setup using the Enhanced Machine Control post processor built in to Fusion 360. A good place to start if you're not sure with CNC programming via Fusion 360 is the NYCCNC Youtube channel.
Operation Instructions
Safety
This is a dangerous tool and should be treated as such. Your safety is your own responsibility. As a guideline, you should wear as a minimum:
- Safety Glasses
- Flying Chips, Broken Tools & loose workpieces are all possibilities
- Ear Defenders
- This machine is seriously loud, you must sit very near to it to monitor the job while it’s running and it’s not uncommon for a cutting cycle to be 30 minutes or longer. Hearing damage is a very real risk. Make sure you also warn others in the CNC room of this too.
Loading your tool
When loading your tool you need to ensure that as much of the shank is contained within the collet as possible. The only exception to this rule is if the job you are running requires a deep cut; then you will need the tool to stick out further.

The video below shows how to load a tool:
Turn on
Turn on the monitor, PC and Control box
The PC should auto boot into linux and automatically log in to the nottinghack
account, if not the password is hackspace
Once in you should see the following desktop, click on the Launch CNC
icon to start LinuxCNC
-
1. Turn on the PC & Control Box
-
2. Click 'Launch CNC' (Penguin Icon)
-
3. Your should now see the
Gmoccapy
interface to LinuxCNC

Emergency Stops
Make sure the physical eStop's have been cleared by twisting them and check that the eStop light on the control box is out.
Reset The linuxCNC software eStop by clicking the red hand icon in the top right corner.
Turn on the machine in the software by clicking the power button just below the software eStop.
The Interface should look like this:
-
4. Software ready to home
Homing
The machine starts-up in joint
mode, in this mode it is possible to move each stepper motor (0,1,2,3) independently but doing so can damage the Y axis.
To use the machine we need to be in world
mode where we operate X,Y,Z axis, LinuxCNC automatically switches to world mode once all the joints have been homed, but it is important to only ever use the 'Home all' option as homing a single joint at a time will damage the Y axis.
To open the Home menu
click the icon in the bottom left corner of the interface. (Target and three arrows)
In the bottom menu now click the Home all Icon (far left)

The machine should now be ready to go.
Important There should be no need to home the machine again however if you need to (due to axis slip or a crash) please close LinuxCNC first and start again, as homing in world
mode is not supported.
-
5. Open the Homing menu (Target and three arrows icon)
-
6. Home all joints
-
7. Machine ready to go
Loading G Code
After you have homed the machine using the instructions above, Click "Enter auto mode to run programs" on the right hand side menu.
On the bottom row of icons you will see a folder icon. Click this to navigate to your ".ngc" G-Code file.
-
8. Enter Auto Mode
-
9. Browse to G-Code file
Setting Zero
G54 is a constant value that is used to provide the offset for the local coordinate system. I.e. It is used to tell the CNC software where you have secured your work-piece to the table (Set Zero). It needs to be set before any program is run!
To set it,
- Enter Manual Jogging mode by pressing the appropriate button on the right hand side or pressing F3 on the keyboard.
- Open the probing menu by clicking on the blue icon at the bottom.
- Use the control arrows to move the gantry so that the centre of the tool is sitting on the point where (X,Y,Z) is (0,0,0) on your CAD model. It is easier to probe one datum at a time. E.g. X, then Y, then Z
- On the bottom bar, press "X=?", "Y=?" OR "Z=?" depending on the direction you have probed and set the zero point.

Accounting for the diameter of the tool can be done by typing in half the tools diameter into the probing menu box. Check its right before running any G-Code by jogging the tool to X=0, Y=0 at a safe Z height; the centre axis of the tool should be over the datum point.
If everything has been set correctly, you should see the preview of your G-Code shift to the correct location.
Running a job
Once G54 is set and the code is loaded simply press the Play button located in the "Auto Mode" menu. Don't leave the job unattended and be ready with the Hoover as a lot of sawdust can be produced.

Example Projects
If you have a project that uses this tool please add it to this list. It would be great to see what other people are using the CNC Mill for!
-
Han Solo in Carbonite CNC
-
Les Plywood Tune-O-Matic Bridge Hardware
-
CNC Workshop for Beginners
-
WW2 Prop Gold