Startrite Bandsaw: Difference between revisions
mNo edit summary |
|||
(12 intermediate revisions by 4 users not shown) | |||
Line 1: | Line 1: | ||
{{Tool | |||
|image=File:Tool Startrite Bandsaw.jpeg | |||
|manufacturer=Startrite | |||
|model=24-S-5 | |||
|obtained=[[Startrite metal bandsaw pledge|Pledge Drive]] | |||
|obtaineddate=June 2015 | |||
|location=Metalworking Area | |||
|team=Metalworking | |||
|induction=No | |||
|defunct= | |||
|defunctdate= | |||
}} | |||
Known as '''Willow'''. | Known as '''Willow'''. | ||
See the back story | ==History== | ||
See the back story on the [[Startrite metal bandsaw pledge]] page. | |||
== Specification == | == Specification == | ||
[[File:Large Startrite Rating Plate.jpeg|thumb|400px|Rating Plate]] | |||
3 | 3 (12") wheels, 5 speed, 24" throat bandsaw. | ||
Cast-iron two-part tiltable table. | Cast-iron two-part tiltable table. | ||
Line 13: | Line 27: | ||
== Usage == | == Usage == | ||
This tool is intended for cutting a range of non-ferrous and non-metallic materials (see the [http://www.altsawsandspares.co.uk/S1%20&%20S5%20Handbook%204E%20WM.pdf handbook]); in the Hackspace, this is intended only for metal cutting, and the blade installed reflects this. | |||
Ferrous (Iron, Steel, Stainless Steel) materials can only be cut provided that care is taken, and no excess pressure is applied. | |||
The band speed should remain set to the slowest for maximum compatibility with a wide range of materials. The Hackspace is not a production workshop, and the higher speeds will only reduce the life of the blades. | |||
== Safety == | == Safety == | ||
Line 19: | Line 37: | ||
== Blades and Maintenance == | == Blades and Maintenance == | ||
Blade length is 3200mm / 126" | Blade length is 3200mm / 126", 1/2" to 3/4" wide. These cost £19 - £25 each. | ||
The first blade bought is a Morse M42 bimetal 10-14tpi [http://bandsawblog.com/variable-pitch-band-saw-blades-when-is-it-used/ varipitch] from [http://www.bandsawblades-direct.co.uk/Bandsaw_Blades_Direct.html Bandsaw Blades Direct] in Heanor. This is a general-purpose production-quality blade for cutting materials between 6mm and 35mm in thickness. | The first blade bought is a MK Morse M42 bimetal 1/2" x 10-14tpi [http://bandsawblog.com/variable-pitch-band-saw-blades-when-is-it-used/ varipitch] from [http://www.bandsawblades-direct.co.uk/Bandsaw_Blades_Direct.html Bandsaw Blades Direct] in Heanor. This is a general-purpose production-quality blade for cutting materials between 6mm and 35mm in thickness. A second, coarser, 3/4" x 6-10tpi [http://bandsawblog.com/variable-pitch-band-saw-blades-when-is-it-used/ varipitch] blade has been bought for trial when the existing blade fails, which we're told should last longer (fewer teeth within the material being cut means that they don't overheat) | ||
Blade Break-In: Extremely Important (from [http://www.mkmorse.com/PDFs/MORSEBANDCAT.pdf MK Morse blade materials]) | |||
The extremely sharp tooth points and edges of new blades must be broken-in before applying full feed pressure to the blade. A good analogy is that of writing with a freshly sharpened wooden pencil. | |||
Recommended Break-In Procedure | |||
* Maintain proper blade speed for the material to be cut. | |||
* Reduce blade feed pressure or feed rate by 50% for the first 50 to 100 square inches of material cut. | |||
* Gradually increase feed pressure or feed rate after break-in to target pressure or rate. | |||
Further information concerning [http://littlemachineshop.com/Info/bandsaw.php blade selection], [http://www.mkmorse.com/PDFs/MORSEBANDCAT.pdf MK Morse blade materials] [http://www.detroitbandsaw.com/store.asp?pid=24064 and troubleshooting]. Possible sources of replacement parts: [http://www.carterproducts.com/band-saw-products/band-saw-wheels-tires tyres and guides] and [http://www.ebay.co.uk/usr/bandsaw-tire-warehouse tyres] | |||
A trial (May - June 2016) of lower cost HSS fixed-pitch blades showed no advantages in cost / lifetime, but showed that one real advantage of the vary-pitch blades is that they don't screech - which the fixed-pitch ones did. | A trial (May - June 2016) of lower cost HSS fixed-pitch blades showed no advantages in cost / lifetime, but showed that one real advantage of the vary-pitch blades is that they don't screech - which the fixed-pitch ones did. | ||
== Recommended Regular Maintenance == | |||
From the [http://www.altsawsandspares.co.uk/S1%20&%20S5%20Handbook%204E%20WM.pdf handbook] | |||
* Weekly | |||
Remove embedded chips from the bandwheel tyres | |||
Clean upper and lower blade guide assemblies and check for wear | |||
* Monthly | |||
Check condition and tension of vee belts (motor drive cabinet) | |||
* General | |||
Clean and lubricate working parts as required. | |||
(The bandwheels have sealed-for-life bearings which do not require further lubrication. | |||
Check that the operating speed is set appropriately for the blade in use (to be determined and documented) and check availability of blades. | |||
[[Category:Tools_and_Equipment]] | [[Category:Tools_and_Equipment]] | ||
[[Category: | [[Category:Metalwork]] |
Latest revision as of 12:29, 29 March 2019
Startrite Bandsaw | |
---|---|
![]() | |
Manufacturer | Startrite |
Model | 24-S-5 |
Obtained | Pledge Drive (June 2015) |
Location | Metalworking Area |
Team | Metalworking |
Induction Required | No |
Tools: all pages • list • Power Tools • Broken tools {{}} |
Known as Willow.
History
See the back story on the Startrite metal bandsaw pledge page.
Specification
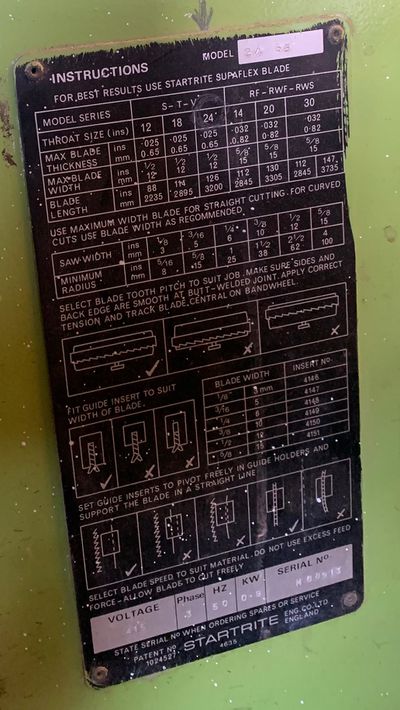
3 (12") wheels, 5 speed, 24" throat bandsaw.
Cast-iron two-part tiltable table.
Powered from 415V three phase supply.
Usage
This tool is intended for cutting a range of non-ferrous and non-metallic materials (see the handbook); in the Hackspace, this is intended only for metal cutting, and the blade installed reflects this.
Ferrous (Iron, Steel, Stainless Steel) materials can only be cut provided that care is taken, and no excess pressure is applied.
The band speed should remain set to the slowest for maximum compatibility with a wide range of materials. The Hackspace is not a production workshop, and the higher speeds will only reduce the life of the blades.
Safety
Blades and Maintenance
Blade length is 3200mm / 126", 1/2" to 3/4" wide. These cost £19 - £25 each.
The first blade bought is a MK Morse M42 bimetal 1/2" x 10-14tpi varipitch from Bandsaw Blades Direct in Heanor. This is a general-purpose production-quality blade for cutting materials between 6mm and 35mm in thickness. A second, coarser, 3/4" x 6-10tpi varipitch blade has been bought for trial when the existing blade fails, which we're told should last longer (fewer teeth within the material being cut means that they don't overheat)
Blade Break-In: Extremely Important (from MK Morse blade materials)
The extremely sharp tooth points and edges of new blades must be broken-in before applying full feed pressure to the blade. A good analogy is that of writing with a freshly sharpened wooden pencil.
Recommended Break-In Procedure
- Maintain proper blade speed for the material to be cut.
- Reduce blade feed pressure or feed rate by 50% for the first 50 to 100 square inches of material cut.
- Gradually increase feed pressure or feed rate after break-in to target pressure or rate.
Further information concerning blade selection, MK Morse blade materials and troubleshooting. Possible sources of replacement parts: tyres and guides and tyres
A trial (May - June 2016) of lower cost HSS fixed-pitch blades showed no advantages in cost / lifetime, but showed that one real advantage of the vary-pitch blades is that they don't screech - which the fixed-pitch ones did.
Recommended Regular Maintenance
From the handbook
- Weekly
Remove embedded chips from the bandwheel tyres Clean upper and lower blade guide assemblies and check for wear
- Monthly
Check condition and tension of vee belts (motor drive cabinet)
- General
Clean and lubricate working parts as required. (The bandwheels have sealed-for-life bearings which do not require further lubrication. Check that the operating speed is set appropriately for the blade in use (to be determined and documented) and check availability of blades.